Project
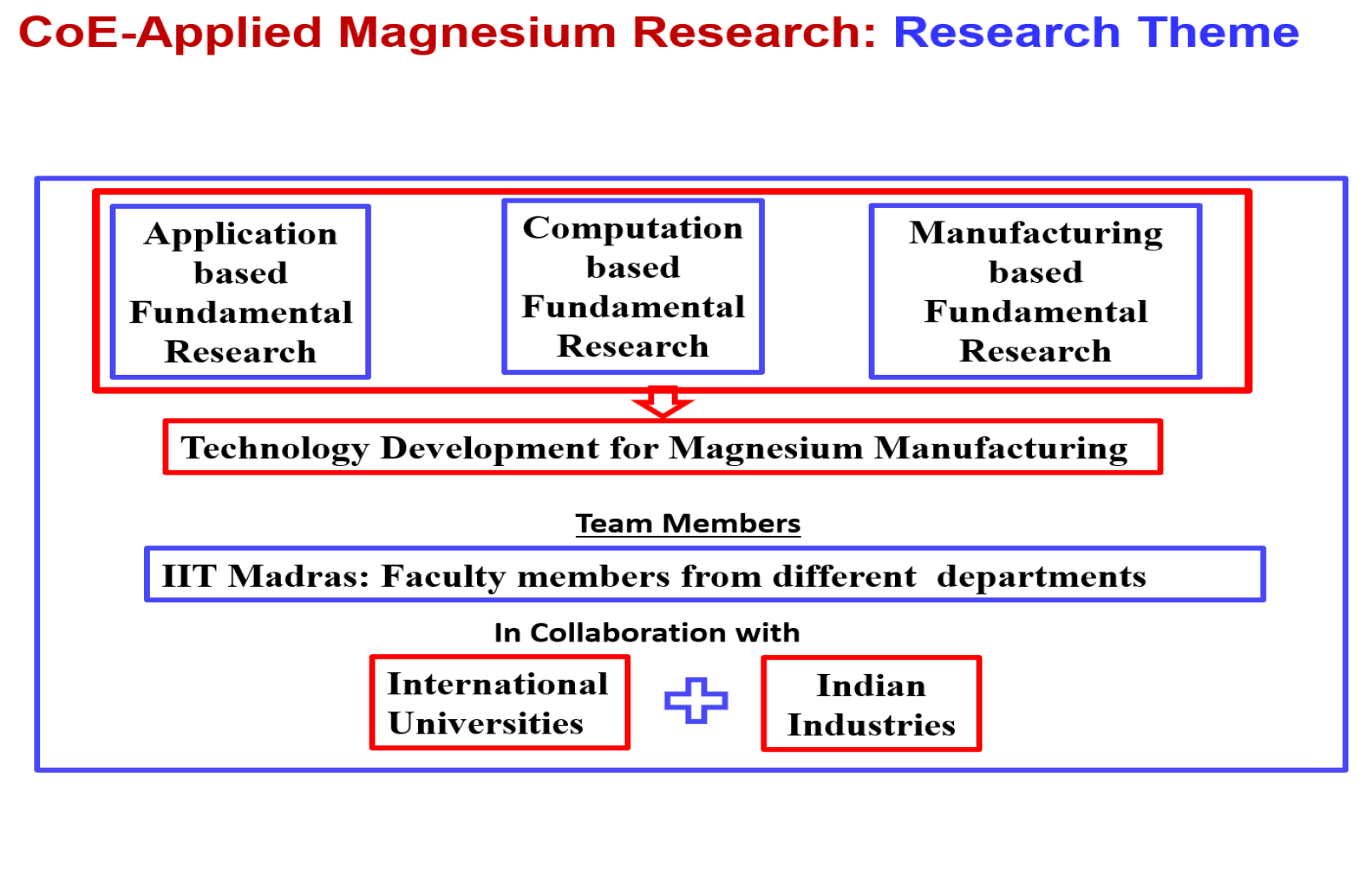

Technology Development based Projects | ||
Project No | Project Title | Contact Person for queries (PI) |
P-1 | Technology development of Mg based in-situ and ex-situ composite manufacturing | Dr. Sushanta Panigrahi |
P-2 | Technology development for Mg based metallic close cell foam manufacturing | Dr. Manas Mukherjee |
P-3 | Technology development for manufacturing high performance engineered Mg alloy sheets | Dr. Sushanta Panigrahi |
P-4 | Technology development for high performance multi metallic Mg based dissimilar sheet manufacturing | Dr. Sushanta Panigrahi |
P-5 | Technology development of Mg- Micro component manufacturing | Dr. Sushanta Panigrahi |
Fundamental Science based Projects | ||
Project No | Project Title | Contact Person for queries (PI) |
P-6 | Crystal plasticity based computational fundamental research (CFR) to establish deformation based micromechanics of Mg alloys | Dr. Anand Krishna Kanjarla |
P-7 | First principle calculation (FPC) based computational fundamental research (CPF) to understand the effect of alloy design on plastic deformation behavior of Mg alloys | Dr. Ilaksh Adlakha |
P-8 | Surface engineering of Mg alloys and their corrosion studies: Experimental and Computational Study | Dr. Lakshman Neelakantan |
P-9 | Forming based technologies to improve formability of Mg alloys | Dr. K. Hariharan |
Project-1: Technology development of Mg based in-situ and ex-situ composite manufacturing
Al metal matrix composites (AMMC) are extensively used in automobiles (Cylinder blocks, pistons, brake discs/drums, drive shafts etc.). Replacing the AMMC with magnesium metal matrix in-situ composites (In-situ-MMMC) will lead to significant weight reduction, as Mg is 40 % lighter than Al. As compared to unreinforced Mg alloy, in-situ MMMC offer higher strength, higher young’s modulus, higher wear resistance and lower tension-compression yield asymmetry. At present, more than 90% of in-situ Mg matrix composites are made via conventional liquid state processing/casting routes. The in-situ reaction in most of the conventional liquid state processes occur in the range of 800 to 1000 °C at a holding/dwell time of 1-2 hours. Since Mg is very reactive and oxidizing material, its oxidation kinetics increases significantly at high temperatures. This leads to several problems such as: (i) molten magnesium tends to oxidize and burn, unless care is taken to protect its surface against oxidation, (ii) high temperature stirring leads to gas entrapment, grain coarsening and elevated porosity and (iii) significant amount of energy is required for melting the metals in conventional furnaces at such high temperatures (800 °C to 1000 °C) and long holding/dwell time (1-2 hours). Therefore, current application of in-situ MMMC in commercial/transportation is almost negligible due to the above-mentioned manufacturing challenges and hence, it is highly essential to develop an alternate liquid state manufacturing route to fabricate such in-situ Mg matrix composites.
In this project, attempts will be made to establish innovative newer technologies to manufacture Mg based in-situ and ex-situ composites in effective, energy saving and time saving approaches.
Project-2: Technology development for Mg based metallic close cell foam manufacturing
Closed-cell metal foams possess a set of unique properties such as high specific strength and stiffness, crash energy absorption, acoustic and vibration damping, etc. Al foams are generally more popular due to the low density of Al and ease of manufacturing. However, Mg foams are more promising because Mg is 35% lighter than Al. Therefore, Mg foam is a potential material for lightweight structural and energy absorption applications.
The proposed project is aimed to develop foam sandwich structure from Mg-based MMMCs. Such sandwich structures promise to possess superior properties compared to other sandwich structures.
Project-3: Technology development for manufacturing high performance engineered Mg alloy
Sheets made up of Steels, Al alloys and Ti alloys are extensively used in various components of automobiles, aerospace, space and other structural applications. Replacing these materials with Mg will result in significant fuel saving, light weighting and CO2 emission reduction benefits. Because of the application potential, Mg alloy sheet development has now become a key research area over the last decade. Due to the inherent HCP crystal structure, Mg alloys cannot be easily rolled as like Al and steel due its limited plasticity. Therefore, currently Mg alloys sheets are developed through direct chill casting followed by multiple passes of hot rolling. This manufacturing process is complicated and involves multiple stages namely molten Mg, direct chill casting, scalping, homogenization, rolling (multiple passes), reheating and final rolling (multiple passes to get thin sheets). Therefore, there is a need to develop Mg sheets using less number of steps. The Mg alloy sheets developed through conventional process consists of coarse-grained microstructure resulting in the poor properties of the developed sheets like high tension/compression yield asymmetry, moderate strength, poor ductility, poor superplastic formability. These sheets also pose strong basal texture which is not favorable for the material to be used for forming applications (like stamping, deep drawing etc.). According to literature, Mg alloys with ultrafine grained (UFG) microstructure shows high strength, reduced tension-compression, yield asymmetry and superplastic formability. Severe plastic deformation (SPD) processes like equal channel angular extrusion, high pressure torsion and friction stir processing routes are primarily used to develop such UFG materials. However, strong crystallographic texture often occurs in the SPD processed UFG Mg alloys which affects the formability. The UFG Mg alloys with random texture is a desirable need for achieving high formability along with other above-mentioned properties. Sheets can be developed via rolling processes, and till now, none of the researchers are successful in engineering UFG microstructure with random texture via rolling based processes.
The proposed project is aimed to establish technologies to manufacture high performance UFG and engineered Mg alloy sheets specific to end applications with less number of rolling passes.
Project-4: Technology development for high performance multi metallic Mg based dissimilar sheet manufacturing
Different combinations of bimetallic sheets (Al/St, Al/Cu, Cu/St etc.) are extensively used in automotive, aerospace, marine and space applications. For example: Al/St bimetallic thin sheets are extensively used in automobile sector for automotive body moldings, drip rails, rocker panels, silencer and other trim components. Al/Cu sheets are widely used in bushing, busbar, utensils, coins, Li-Fe taps, switch panels etc. Similarly tri metals have wide applications such as: Ti/Al/Ti in aerospace, Al/Ti/Al in spacecraft, Al/St/Al in automobiles, Ti/St/Ni in fuel cell, Ni/St/Cu in bottom battery cap, Al clad (Al/Al alloy (3003 or 2xxx or 7xxx)/Al). Among all the bi-metallic combinations Al/St is most widely used in automobile structural components. In case of tri-metal combinations, Al clad is the most popular one where high strength Al alloy is used as a core and corrosion resistant Al is used as clad in both sides of core. Al clad materials are extensively used in automobile heat exchangers; aircraft-structural parts, skin, wings, fuselage, cowls etc.; spacecraft-fuel tanks, nose, structural panels, radiator panels etc. In both Al/St and Al clad materials, Al is primarily used for light weighting. In all the above mentioned bimetallic or tri metallic combinations, the materials are mostly either FCC or BCC and hence have significant ductility. Therefore, these bi-metals and tri-metals were successfully developed by conventional roll bonding/explosive bonding/laser cladding. Mg is 40 % lighter than Al and hence replacing Al with Mg in both bimetal and trimetal combinations will result in significant light weighting potential. However, Mg is having HCP crystal structure which resist for plastic deformation. Therefore, there are challenges to bond Mg with other metallic materials via existing plastic deformation-based processes like explosive bonding and roll bonding. Moreover, explosive bonding and roll bonding manufacturing routes often shows: (i) poor interfacial bonding, (ii) less mechanical strength and (iii) undesirable anisotropic property because of severe texture.
The proposed project is aimed to establish innovative technologies to manufacture high performance multi-metallic dissimilar sheets
Project-5: Development of Mg- Micro component manufacturing
Micro-components have wide application in MEMS and transportation sector. Being the lightest weight metallic material, Mg alloy find its suitability in several micro-components such as micro gears, microturbines etc.in transportation/mobility sector. However, in Mg due availability of limited number of slip system at room temperature, makes Mg a challenging choice for any kind of forming application. On the other hand, forming of components in micro domain(<1mm) itself is a challenging task due size effect, complex tool design, lack of repeatability and difficulty in handling of micro part etc.. Therefore there is a need to study the micro scale deformation behavior of Mg alloys. One of the possible route to overcome the size effect related issue is to change the deformation mechanism of Mg alloy form slip based to GB sliding based, whereby eliminating size effect which is a slip activated phenomena in order to obtain defect free Mg microformed components. The current work aims to overcome the above-mentioned challenges by engineering the microstructure and studying the superplastic behavior of the Mg alloys in order to develop a route to mass produce Mg based micro components.
Project-6: Crystal plasticity based computational fundamental research (CFR) to establish deformation based micromechanics of Mg alloys
The distribution of local strains/stresses within a microstructure is important in explaining the ductility behavior of Mg alloys. The high strength in the alloy(s) that are being developed as part of CoE will often consist of elements such as rare earths, transition elements, precipitates and so forth. The challenge is not only to understand the deformation behavior of the individual precipitates, but how they might potentially change the matrix behavior. Will they suppress deformation twinning altogether or will they change just the size distribution of the latter, which in turn affects the yielding and the work hardening behavior. We will tackle this issue using combined experimental and crystal approach. The main objective of this proposal is to strengthen Mg alloys by understanding the physical mechanisms responsible for strength by combining experiments and simulations at multiple length scales. We will study in detail the role of various alloy elements and precipitate distribution on the yield strength, plastic anisotropy, and the work hardening behaviour. We plan to identify suitable alloying elements that decrease the plastic anisotropy in Mg alloys using first principles calculations. Next, the individual interaction between different types of dislocations and the various precipitates using atomistic modelling will be examined. The homogenized response of the dislocation-precipitation interaction will be implemented in crystal plasticity to develop models with accurate predictive capabilities. The experimental validation of the computational efforts will be performed using synchrotron/neutron/electron diffraction experiments. The state of the art in this field is about combining cutting edge experiments and high fidelity modelling works. As far the proposed topic is concerned: there are three distinct approaches: (i) performing in-situ deformation experiments using high energy synchrotron/neutron diffraction experiments combined with mean field and full field modeling efforts to understand the bulk statistical behavior (ii) Performing quasi/interrupted-insitu experiments to understand the local micromechnical fields and gain insight into the role of spatial aspects of the microstructure in strain localization (iii) Utilizing simulations to perform virtual experiments to scan the large microstructural and property space and to come up design/processing guidelines for experimentalists.
Project-7: First principle calculation (FPC) based computational fundamental research (CPF) to understand the effect of alloy design on plastic deformation behavior of Mg alloys
The adaptation of Mg alloys to large scale applications has been restricted primarily due to their limited room temperature plasticity, that stems from the limited number of active slip systems at room temperature, which leads to failure in polycrystalline Mg-alloys at ambient conditions, thereby limiting the formability of Mg alloys In an attempt to improve the strength and formability of Mg at room temperature, the effects of various solute additions, especially rare earth elements such as yttrium (Y), lanthanum (La) [4] etc. was found to be viable method of improving room temperature ductility. For instance, in Mg-3 wt% Y alloys the room temperature ductility improved due to the activation of additional pyramidal <c+a> slip system. This was attributed to an increase in the critical resolved shear stress (CRSS) of the basal slip system due to the addition of Y, thus the activation probabilities of basal and pyramidal slip systems becoming equal. The addition of Al to Mg alloys was found to enhance ductility was reported due to increased resistance to grain boundary sliding, as well as a decrease in the basal plane stacking fault energy. Similarly, the addition of Ce, Li and Zn to Mg alloys was found to improve the room temperature ductility, due to the activation of non-basal <c+a> and prismatic slip systems. On the other hand, tensile tests on extruded Mg-Zn alloys show that the yield strength increases with Zn addition compared to pure Mg due to solid-solution strengthening in Mg-Zn alloys [9]. Such divergent results reflect the ambiguous understanding of the effects of different solute atoms on the plastic deformation in Mg. Computational tools can provide valuable insights into the effect of solute addition on the plastic deformation of a material. The first principles calculations have generally focused on calculating ideal strength (maximum attainable stress) and generalized stacking fault energy (GSFE), which closely relates to the dislocation properties and plasticity of the material. For instance, the GSFE curve can quantify the critical resolved shear stress (i.e. the shear stress that needs to be overcome by a dislocation to move), dislocation core width, stacking fault width and nature of dislocation dissociation. Similarly, the strength of a real crystal is affected by various defects, but the ideal shear strength/resistance for a defect free crystal offers fundamental suggestions regarding the dislocation nucleation and shearability of the crystal, i.e., minimum shear stress required to instigate plastic deformation in a pure crystal with no defects. Therefore, with the help of first principles calculations we intend to provide a roadmap for identifying solute elements that can improve the room temperature ductility of Mg alloys, thereby accelerating the development of novel alloys.
Project-8: Surface engineering of Mg alloys and their corrosion studies: Experimental and Computational Study
The poor corrosion resistance of Mg alloys has been one of the primary reasons for the limited large-scale applicability. From an electrochemical perspective, the inability of Mg alloys to form a stable passive layer in combination with high electrochemical activity (i.e., lowest standard reduction potential among all structural metals (approximately −2.4 V versus standard hydrogen electrode), resulting in higher corrosion rate upon contact with water, resulting in higher corrosion rate upon contact with water. However, the accurate characterization method for estimation of corrosion behavior of Mg alloys has not been developed. Therefore, this proposal would explore a novel, sensitive and precise technique as an alternative to volumetric method of hydrogen collection to assess Mg alloy corrosion rate. In order to improve the strength, corrosion resistance and biocompatibility, the metallurgists have developed Mg alloys with addition of various elements like Al, Si, Ca, Sr, Zn, Mn, Ti, Ag, Th, Y, Nd, and Gd etc. Surface modification of Mg alloys is imperative if the mechanical properties of the alloy are to be maintained. Usually components of Mg and Mg alloys are subjected to certain procedures such as machining, grinding, degreasing, and pretreatment before surface modification. Conversion treatments in acidic solutions based on Cr (VI) are typically used for passivation of Mg alloys. However, chromium trioxide and dichromates are banned, hence appropriate alternatives are to be developed. This is especially inevitable for its application in aerospace and automotive applications. Hence this proposal will attempt for viable alternative coating technology to protect Mg alloy surfaces. The issue is further worsened through unavoidable engineering design constraints, where Mg alloys are frequently coupled to electrochemically dissimilar structural components. In service, these couples lead to preferential galvanic corrosion which is accelerated by mechanical loading in harsh corrosive environments, (such as: sulfides, hydroxides, bicarbonates, CO/CO2, chlorides and ammoniacal solutions), thereby undermining the structural integrity of transport platforms by drastically decreasing the failure life In general, there is a lack of consensus on the role of mechanical deformation plays in the corrosion behavior. Therefore, understanding the role of mechanical loading on the galvanic corrosion behavior is highly relevant to the long-term goal of increasing the applicability of Mg alloys. Moreover, assessing the combined effects of mechanical loading and corrosion behavior on the structural integrality of galvanic joints using experimental electrochemical characterization has several limitations. Therefore, the proposed project is intended to employ numerical methods to examine the corrosion behavior for a galvanic joint subjected to mechanical loads is highly relevant in improving the life of structural joints that are subjected to harsh conditions.
Project-9: Forming based technologies to improve formability of Mg alloys
The present use of magnesium as a lightweight material in automotive and aerospace industry is scarce due to the challenges in manufacturing and assembly of magnesium sheet components. The poor formability of magnesium alloys in room temperature is one of the major bottlenecks for magnesium sheet components. In this project, attempts will be made to evaluate and improve formability of Mg alloys at room temperature using novel roboforming process. The outcome, in addition to room temperature formability improvement, provide insights for development of new Mg alloy system. Warm forming is widely used to form Mg alloys. Systematic investigations of warm forming process correlating the evolution of crystallographic texture is essential to engineer the initial microstructure and process.The poor formability of Mg alloys is mainly due to HCP crystal structure and limited slip systems. Several new alloy systems have been developed in the past to improve the mechanical properties by optimizing composition and thermomechanical processing. Alloy design for Mg is an active research field. Apart from alloy composition engineering the microstructure and texture has improved the strength-ductility properties. In tandem were the research on improving formability of Mg using modified manufacturing processes. Due to poor room temperature formability, warm forming is preferred for Mg alloys. Warm forming is been studied in conjunction with traditional and advanced forming processes such as incremental forming, hydroforming etc. Of specific interest is incremental forming process with different heating sources and tool path. It is proposed to use robot forming process for magnesium forming. While incremental forming process has been studied both at room and elevated temperature, only limited attempts have been made to correlate the texture evolution during incremental forming. By correlating the texture(both bulk and micro texture) evolution, the microstructure and strain path can be potentially optimized to facilitate room temperature forming of Mg alloys.
The formability studies in warm forming has been focused on the traditional forming facilities. In the recent years, time dependent formability improvement using servopress has been found promising.The mechanism for formability improvement using servo press is not established. A complex interaction between viscoplastic material behaviour, friction and elastic springback contributes to formability improvement. It is envisaged that by appropriate understanding of the mechanism and path planning it is possible to improve the room temperature formability of Mg alloys. It is intended to explore the use of servo press to improve room temperature formability and/or to reduce the deformation temperature during warm forming.
Expected deliverables of the research
The key objective and expected deliverables of the Applied Magnesium Research Group (AMRG) is to establish technologies to:
improve structural efficiency (mechanical, forming, corrosion resistance etc.) of Mg alloys,
develop high performance Mg based alloys, composites (both in-situ and ex-situ), foams etc. and establish their manufacturability,
develop manufacturing strategies for Mg high performance sheet development, Mg based multi-metallic sheet development, Mg wrought alloy development, Mg forming technology development
improve the manufacturing potential of existing Mg alloys etc.
In order to establish the technologies, the AMRG is focused to lay the foundation of scientific base via 1st principle based and crystal plasticity based numerical modeling approaches, theoretical studies, alloy design and microstructural engineering principles.
Current status
A. Currently, the Applied Magnesium Research Group (AMRG) is actively involved in the above mentioned 9 (nine) projects.
B. The AMRG members have rich experience in successfully carrying out several sponsored external projects related to Magnesium Technologies and allied research. Few of such funding agencies are DST, MHRD, DSIR, ISRO, DRDO, Ministry of Heavy Industries, Renaults Nissan, Mahindra & Mahindra, Rane N & K Steering Systems Pvt Ltd, Aditya Birla Groups, Tata Steels etc.)
C. The AMRG members have published their Applied Magnesium based research innovation in several high impact research publications. Few of such publications are shown below:
S.K. Sahoo and S.K. Panigrahi, “Hot deformation behavior and processing map of ZE41 Mg alloy and in-situ sub-micron sized TiB2/ZE41 composite”, Journal of Magnesium and Alloys, (I.F- 10.00), Elsevier Publ. Accepted (2021).
S, Mishra, F.Khan MD, S.K.Panigrahi, “A crystal plasticity-based approach to establish role of grain size and crystallographic texture in the Tension – Compression yield asymmetry and strain hardening behavior of a Magnesium-Silver-Rare Earth alloy ” Journal of Magnesium and Alloys, (I.F- 10.00), Elsevier Publ. Accepted (2021).
A. Kumar, A., Md, F.K., S.K. Panigrahi, G.P. Choudhury, Microstructural evolution and corrosion behaviour of friction stir-processed QE22 magnesium alloy, Corrosion Reviews (I.F-2.4), Freund Publishing House Ltd, 39 (2021) 351-360, link.
Ansari. N, B.Tran, W. J. Poole, S. S. Singh, K.Hariharan and J. Jain, “High temperature deformation behavior of Mg-5wt.%Y binary alloy: Constitutive analysis and processing maps”, Materials Science and Engineering A (I.F-5.3) , Elsevier Publ. 777, 139051 (2020).
G.R Argade, S.K Panigrahi, R.S Mishra, Aging response on the stress corrosion cracking behavior of wrought precipitation-hardened magnesium alloy, Journal of Materials Science (I.F-4.2), Springer Publ., 48 (2020) 5633-5644,link
S. Bhogi, B. Muduli, M. Mukherjee, “Effect of Mg addition on the structure and properties of Al-TiB2 foams”, Materials Science and Engineering A (I.F-5.3), Elsevier Publ., 791(2020) 139581. link
S.K Panigrahi, R.S Mishra, R.C Brennan, K. Cho, “Achieving extraordinary structural efficiency in a wrought magnesium rare earth alloy” Materials Research Letters (I.F-7.5), Taylors & Francis Publ., 8 (2020) 151-157, link.
S.K Sahoo, B.N Sahoo, S.K Panigrahi*, Effect of in-situ sub-micron sized TiB2 reinforcement on microstructure and mechanical properties in ZE41 magnesium matrix composites, Materials Science and Engineering A (I.F-5.3), Elsevier Publ., 773 (2020) 138883, link.
B.N. Sahoo, S.K. Panigrahi*, “Deformation behavior and processing map development of AZ91 Mg alloy with and without addition of hybrid in-situ TiC+ TiB2 reinforcement” Journal of Alloys and Compounds (I.F-5.3), Elsevier Publ., 776 (2019) 865-882, 88 link.
B.N.Sahoo, S.K. Panigrahi*, “Development of wear maps of in-situ TiC+ TiB2 reinforced AZ91 Mg matrix composite with varying microstructural conditions” Tribology International (I.F-4.9), Elsevier Publ., 135 (2019) 463-477, link.
C. Paramatmuni, A.K. Kanjarla, “A crystal plasticity FFT based study of deformation twinning, anisotropy and micromechanics in HCP materials: application to AZ31 alloy” International journal of Plasticity (I.F-7.1), Elsevier Publ., 113 (2019) 269–290. link
MD F. Khan, G.M. Kartik, S.K. Panigrahi*, G.D.J Ram, “Friction stir processing of QE22 magnesium alloy to achieve ultrafine-grained microstructure with enhanced room temperature ductility and texture weakening”, Materials Characterization (I.F-4.4), Elsevier Publ., 147 (2019) 365-378,link.
S. Bhogi, M. Mukherjee, “Processing and characterization of Al foams stabilized by Mg”, Transaction of the Indian Institute of Metals (I.F-1.5), Springer Publ., 72(2019), 1417-1420. link
Adlakha I., Gholami Bazehhour B., Muthegowda N., Solanki K.N. “Effect of mechanical loading on the galvanic corrosion behavior of a magnesium-steel structural joint”, Corrosion Science (I.F-7.2) 133, 300-309 (2018). link.
B.N.Sahoo, S.K. Panigrahi*, “A study on the combined effect of in-situ (TiC-TiB2) reinforcement and aging treatment on the yield asymmetry of magnesium matrix composite” Journal of Alloys and Compounds (I.F5.3), Elsevier Publ., 737 (2018) 575-589, link.
B.N.Sahoo, MD F. Khan, S.K. Panigrahi*, G,D. Janakiram, “Microstructural modification and its effect on strengthening mechanism and yield asymmetry of in-situ TiC-TiB2/AZ91 magnesium matrix composite” Materials Science and Engineering A (I.F-5.3), Elsevier Publ., (2016) 724 (2018) 269-282, link.
B.N.Sahoo, S.K. Panigrahi*, “Effect of in-situ (TiC-TiB2) reinforcement on aging and mechanical behavior of AZ91 magnesium matrix composite”, Materials Characterization (I.F-4.4) Elsevier Publ.,, 139 (2018) 221-232, link.
Garg P., Adlakha I., Solanki K.N. “Effect of solutes on ideal shear resistance and electronic properties of magnesium: A first-principles study”, Acta Materialia, (I.F-8.2) 153, 327-335 (2018). link
MD F. Khan, S.K. Panigrahi*, “Achieving excellent super plasticity in an ultrafine-grained Magnesium QE22 alloy at both high strain rate and low-temperature regimes”, Journal of Alloys and Compounds (I.F-), Elsevier Publ., 747 (2018) 71-82, link.
Gholami Bazehhour B., Adlakha I., Solanki K.N. “The role of static and cyclic deformation on the corrosion behavior of a magnesium-steel structural joint”, Journal of Materials Science (I.F-4.2), Springer Publ., (2017). link
J Jain, P Cizek and K Hariharan, “Transmission electron microscopy investigation on dislocation bands in pure Mg”, Scripta Materialia,(I.F-5.6), Elsevier Publ. 130, 133-137 (2017).
S. Bhogi, M. Mukherjee, “Foam stabilization by magnesium”, Materials Letters (I.F-3.4), Elsevier Publ., 200(2017), 118-120. link
A. Tripathi, A. Tewari, A. K. Kanjarla, N. Srinivasan, G. M. Reddy, S. M. Zhu, J. F. Nie, R. D. Doherty, I. Samajdar, “Microstructural evolution during multi-pass friction stir processing of a magnesium alloy” Metallurgical & Materials Transaction A (I.F-2.6), Springer Publ., 47, (2016) 2201–2216.link
B.N. Sahoo, S.K. Panigrahi*, “Synthesis, characterization and mechanical properties of in-situ (TiC-TiB2) reinforced magnesium matrix composite” Materials & Design (I.F-5.3), Elsevier Publ., 109 (2016) 300-313, link.
F. Khan MD, S.K. Panigrahi*, “Achieving excellent thermal stability and very high activation energy inn an ultrafine-grained Magnesium Silver Rare Earth (QE22) Alloy prepared by friction stir processing” Materials Science and Engineering A (I.F-5.3), Elsevier Publ., 675 (2016) 338-344, link.
MD F. Khan, S.K. Panigrahi*, “Age hardening, fracture behavior and mechanical properties of QE22 Mg alloy” Journal of Magnesium and Alloys (I.F-10.0), Elsevier Publ.,3 (2015) 210-217, link.
M. Arul Kumar, A.K. Kanjarla, S.R. Niezgoda, R.A. Lebensohn, C.N. Tomé, “Numerical study of the stress state of a deformation twin in magnesium” Acta Materialia (I.F-8.2) , Elsevier Publ., (2015) 349–358.link
A. Mohan, S. K. Panigrahi, R. S. Mishra, R. Verma, “Influence of strain and strain rate on microstructural evolution during superplasticity of Mg-Al-Zn sheet” Journal of Materials Science (I.F-4.2), Springer Publ., 48 (2013) 5633-5644,link.
L. Balogh, S.R. Niezgoda, A.K. Kanjarla, D.W. Brown, B. Clausen, W. Liu, C.N. Tomé, “Spatially resolved in situ strain measurements from an interior twinned grain in bulk polycrystalline AZ31 alloy” Acta Materialia (I.F-8.2), Elsevier Publ., 61 (2013) 3612–3620. link
W. Yuan, S.K. Panigrahi, R. S. Mishra, “Achieving high strength and high ductility in friction stir processed cast magnesium alloy” Metallurgical & Materials Transaction A (I.F-2.6), Springer Publ., 44 (2013) 3675-3684, [link]https://doi.org/10.1007/s11661-013-1744-5).
G.R. Argade, S.K. Panigrahi, R.S. Mishra, “Effects of grain size on the corrosion resistance of wrought magnesium alloys” Corrosion Science (I.F-7.2), Elsevier Publ., 58 (2012) 145-151, link.
G.R. Argade, K. Kandasamy, S.K. Panigrahi, R.S. Mishra, “Corrosion behavior of a friction stir processed rare-earth added magnesium alloy” Corrosion Science (I.F-7.2), Elsevier Publ., 58 (2012) 321-326, link.
S. K. Panigrahi, K. Kumar, R. S. Mishra, R. DeLorme, B. Davies, R. A. Howell, K. Cho, “Transition of deformation behavior in an ultrafine grained magnesium alloy” Materials Science & Engineering A (I.F-5.3), Elsevier Publ., 549 (2012) 123-127, link.
S. K. Panigrahi, R. S. Mishra, K. Kumar, R. DeLorme, B. Davies, R. A. Howell, K. Cho, “A study on combined effect of forging and ageing in Mg-Y-RE magnesium alloy” Materials Science & Engineering A (I.F-5.3) , Elsevier Publ., 530 (2011) 28-35, link.
W. Yuan, S. K. Panigrahi, J.Q. Su, R. S. Mishra, “Influence of grain size and texture on Hall-Petch relationship for a magnesium alloy” Scripta Materialia (I.F-5.6), Elsevier Publ., 65 (2011) 994-97, link.
Collaborations
International Collaborations
Prof. Guillaume Racineux (Ecole Centrale Nantes, France)
Prof. Surendra Marya (Ecole Centrale Nantes, France)
Prof. Kiran Solanki (Arizona State University)
Prof. Nikhilesh Chawla (Purdue University
Prof. Suveen Nigel Mathaudhu (University of California Riverside)
Prof. Manoj Gupta (National University of Singapore, Singapore)
Prof. John Banhart (Helmholtz-Centre Berlin, Germany)
Dr. Francisco Garcia-Moreno (Helmholtz-Centre Berlin, Germany)
Societal impact
Increasing usage of magnesium alloys in automobile industry can lead to significant weight reductions leading to increased fuel efficiency. This is particularly important because of the need to reduce CO2 emissions and meet the challenge of global warming and climate change. Similarly development of novel Mg based biomaterials is critical for affordable health care and improving quality of human life. Hence the proposed Center is expected to be very socially relevant.
Sustenance statement
The long-term sustenance of the center depends upon Indian industry, sponsored research projects and bilateral international projects. A center for magnesium research is first of its kind in the nation and it caters to a range of industry such as automotive, aerospace, space and bio medical applications. The key objective of the center is to overcome the challenges in adopting Mg alloys by systematic research on suitable alloy development and microstructure engineering. The outcome aims to replace other widely used light weight materials such as Aluminium and composites. Many industries have shown interest in the outcome through their ‘Letter of Support’. The center aims to generate fund through its research outcomes that may facilitate the industry to use Mg alloys. The center also proposes a novel economic thermomechanical processing route through which the cost of production of Mg alloys will be significantly reduced. This research activity jointly identified with metal industry will scale the Mg production in the nation. The increased throughput of Mg and the respective utilization will need application specific solutions. Owing the advantage of being the first and only Magnesium research centre in the nation, it is expected that the center through its systematic studies will be in a position to generate funding to mitigate challenges involved in commercialization.
All the faculty members are engaged in conducting sponsored research projects both at national and international levels. New proposals for Mg research will be made to these funding agencies for sustenance of the center. The international collaborations in the center will generate new proposals for furthering the activities of the center through bilateral exchange programmes and joint international proposals.