Project
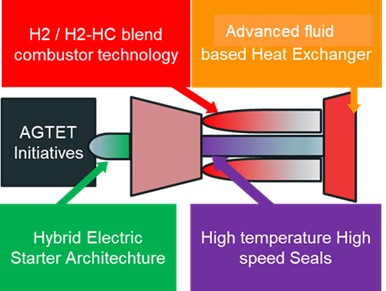
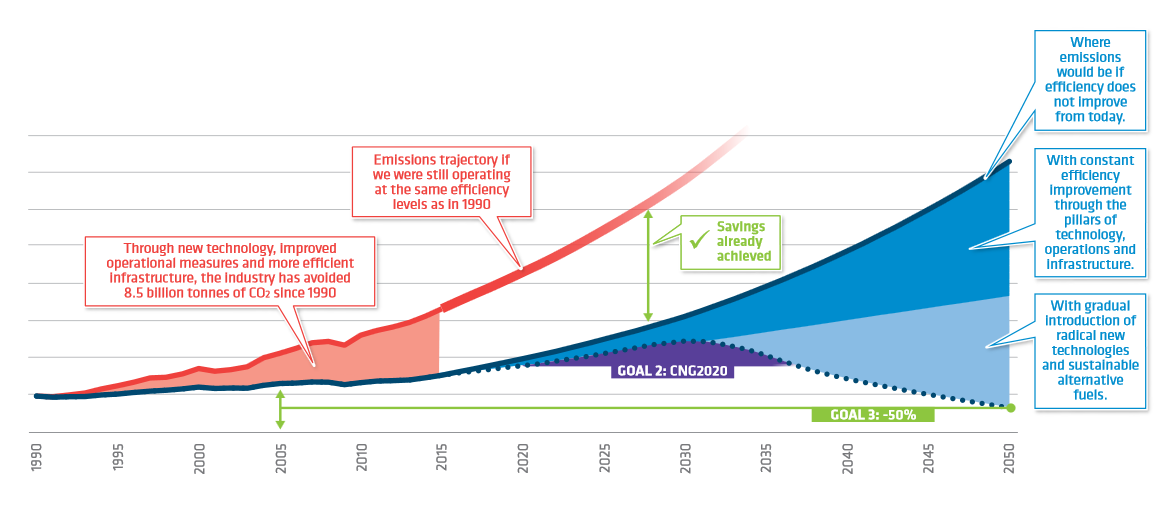
Vertical A:
Futuristic Fuel Based Combustion -This vertical will study H2 and SAF for Gas Turbine combustors. Fundamental aspects of combustion technologies related to these fuels will be assessed for sustained combustion & futuristic environment regulations.
Vertical B:
Thermal management of GT engines – Adapting several innovative heat transfer techniques and advancement in manufacturing technologies to develop compact, high performance next-gen heat exchangers including use of advanced fluids for heat exchangers in future gas turbine engines.
Vertical C:
Seals and Rotor dynamics for next Gen engines- Concurrent development of architectures needed to support the technologies. Understanding the seal behavior with rotor dynamics, and optimizing the seal for a new operating regime, corresponding to hydrogen based fuels.
Vertical D:
Hybrid electric components - Hybrid electric components reducing usage of core GT air and increasing design flexibility.
The four verticals will leverage the latest manufacturing advancements like additive manufacturing, to enable more complex designs for maximum performance. The advantage of all the verticals being under one roof is to enable a wholistic approach to technology development which can be integrated into future jet engines.
Vertical A :
Main objective is to realize advancements in combustion technology to meet Emissions, Operability and Durability requirements for Hydrogen, H-C blends & SAF through component testing, laser diagnostics and model development.
The Centre will establish state of art facility for rig testing, modelled as a plug and play facility for industrial design. Advanced testing capabilities augmented by laser diagnostics makes this a unique facility. Overall vision is captured below:
- Capability of continuous testing upto 1 kg/s at a max of 10 bar & 600 K.
- Expand flow capability beyond 10 bar, 1kg/s and up to 800 K.
- Blending station: Ability to blend fuels (H2, H2-HC) at desired volume ratio.
- Testing capability: Ability to test industry scale configurations at varying air-to-fuel ratios, fuel blends, Pressures/Temperatures.
- Advanced laser diagnostics: PIV, acetone PLIF, NO PLIF, OH PLIF, OH Chemiluminescence, H2O TDLAS.
An optically accessible rig will be developed for visualizing flame and generating benchmark quality data for flame characterization. Benchmark flame data will be used for developing & validating CFD methods that can serve as design tool. On the modeling front, reduced mechanism set (valid till 60 bar & 1500K) for H2, H2-HC and alternative fuels will be recommended, to ensure practical application of CFD methods for industrial scale application.
Vertical B:
Main objective is to develop Next Generation Heat Exchangers using advanced fluids. In H2 powered gas turbine, the specific fuel energy of H2 poses challenges in the thermal management in combustors, primarily due to gas temperatures going above 2000K compared to a conventional gas turbine.
This project aims at using secondary coolants at a select location of GT and advanced heat exchangers for oil cooling and fuel preheating leveraging advanced manufacturing options. Focus is on using conventional and advanced manufacturing methods like additive and the materials will be Co-Cr, Steel alloys, Al-alloys, Ti-Alloys, Nickel based alloys and some refractory alloys such as Niobium, Tantalum and SiC based alloys.
Goal is to develop a testing facility that augments the design of high temperature capable compact heat exchangers suitable for H2 powered GT engines. It requires development of state-of-the-art of testing facility suitable for handling advanced fluids as a secondary fluid while primary could be other liquids such as Oil, Water, Air and Other Refrigerants. The testing facility will be modular for coupon level testing and for prototype testing that fits in H2 powered gas turbine.
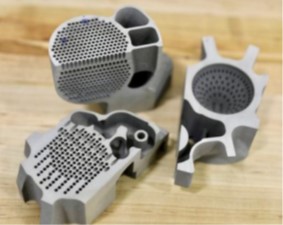
Courtesy: GE Additive
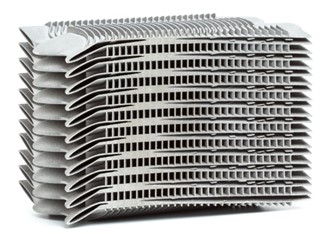
Courtesy: GE Additive
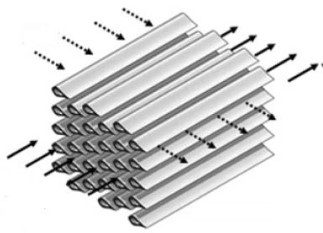
Courtesy: GE Additive
Figure-1 3D printed examples of various flow-path configurations
Vertical C:
The objective of this vertical is to develop & optimize state of art seal technologies, estimate seal rotordynamic coefficients and develop state of art CFD models to estimate and predict the seal rotordynamic parameters. This project aims to test current and future seal concepts and configurations to be used in future aviation gas turbines. The primary scientific contribution from the investigations is to develop new technology seal designs, evaluate thru testing rotordynamic parameters like cross axis stiffness to improve rotordynamic design and develop CFD methods.
This project plans to build a rotating seal Test Rig, perform tests on multiple seal configurations, gather data and use them for CFD model development and validation. The scope of test will include experiments with various seal configurations, various operating speeds, inlet conditions (including heated air) and clearances. The final phase of the project aims at developing new seal designs that will minimize the cross-axis stiffness.
The data will help understand the rotordynamic behavior of rotors that are subject to reduced cross axis forces developed across the seal under a variety of operating conditions/environments. Further the CFD models will also provide guidance on use of seal parameters in new engines and offer additional insight into rotor operations. The new seal designs will foster better designs of rotors from a rotordynamics perspective. The seal rotordynamic parameters would have been established for aviation industry specific seals and operating conditions and provided state of art CFD models for evaluation of seal specific parameters. New seal designs that do not affect engine performance but provide better rotrodynamic performance are envisaged.
Vertical D:
Development of more electric aircraft systems. To reduce carbon footprint and the increase fuel burn in an aircraft required more electric architecture with integrated functionality. In current aircraft architecture, engine starter and electric power generation systems are integrated in an electric machine and acts extremely reliable starter generation system, reduces significant fuel burn and weight of the aircraft. Development of efficient hybrid electric system could take more functionalities eventually and thus reducing weight and fuel consumption.
This project aims at developing, designing, prototype manufacturing and testing of an Electric starter / generator, for specification that matches a commercial aircraft engine and additionally the Electric machine will help to do the engine turning system ( ETS) that improves engine operability. This hybrid system will help to reduce sub system components and weight in the aircraft.
Develop an Electrical Machine (EM) which can operate as electrical Starter / Generator with very high efficiency, lower sub system and lower weight. This EM will be controlled using a bidirectional converter using SiC technology to optimize size and improve efficiency. This bidirectional converter operates electrical machine as a motor during cranking of the engine and as a generator after the engine starts producing the mechanical power. When operated as motor, it must provide enough torque to overcome the peak drag torque during engine start cycle. This converter acts also as an Active Rectifier when the engine is generating mechanical power and rectifies the power produced by the Electric machine into DC output.
This electrical machine also have the Engine Turning System (ETS) functionality to facilitate extended low-speed motoring of the engine. ETS is required to Rotate engine core after engine is shut down to thermally equalize rotor shaft and prevent oil temperature rise.
Testing of product to prove functionality as laid out in requirement specification. Due to aircraft engine application, product will have stringent requirement on power, weight, size, cooling and safety requirements. This pushes the existing boundaries on power densities, cooling technology and bearing design. This product development would involve using of high-performance material to improve electrical, mechanical and thermal performance. Additive manufacturing to develop inbuilt complex cooling holes, Specialty tool development for assembly and integration of high precision machinery. The prototype development is planned in Phase 2 (after 2 years), while design will be done in phase 1.
Proposed technology development aims at achieving Technology Readiness Level (TRL) 3 for this technology in Phase 1 and TRL 5 in phase 2. The current electric machine for this application is at TRL 1/ TRL2 level.
Expected deliverables of the research
Technology Readiness for Aviation Combustors for High Hydrogen content fuels, and SAF, and its test facility.
Next Gen Heat Exchangers using Advanced Fluids for Hydrogen fired GT Engines.
Develop optimised state of the art seal technologies, estimate seal rotor dynamic coefficients for stability and develop state of the art CFD models.
Development and Prototypes of Next Gen hybrid electric products for Gas Turbines.
Current status
Infrastructure/ facilities developments for individual verticals underway.
Procurements and preliminary designs ongoing.
Working closely with GE Aviation’s Bangalore Engineering Center.
Collaborations
Industrial collaborations
- GE Aviation, GE Global Research Campus, Bangalore is collaborating with this center by providing industry experience. They also contribute towards development support and fabrication.
Societal impact
Sustenance statement
This center can sustain itself through active collaborations with industry (like GE Aviation). The facilities developed here can be used by all gas turbine/ heat transfer/ rotors industry for research and development purposes. The full center when established in the second phase, will become a unique center with all the relevant verticals required for testing the gas turbine engine technologies, in relevant parameter space, while maintaining the academic rigor.
While the core activities are geared towards development of a new architecture for gas turbine engines, the developed technologies from each of the verticals may be applicable to other industries as well. Example, hydrogen combustor, combustion model and heat transfer solutions can be applied in energy sector and automotive sector, as well.
Technical/ Scientific Progress
New work done in the project
Vertical A: The high pressure rig has been designed. The team is testing it for safety checks. The tender process for fabrication will start for it after it clears safety requirements. The combustor preliminary design is complete and detailed design is underway. The flow conditions and flow geometry has been finalized. Flame characterization is planned using laser diagnostics at multiple equivalence ratios and H2/Hydrocarbon blends. The required optical diagnostics planes have been finalized. Design of flow control system for the combustor is being designed. There are several options for this, and we will have to find the one that will fit our budget. The compromise will be in terms of ease of operation versus the cost. Thus all the system designs are being pursued, at the moment. Vertical B: A complete P&ID of the transcritical CO2 testing facility setup has been finalized. IIT M team has finished procurement of sensors and major components required for the test rig. Complete mechanical integration of the CO2 loop is expected to be complete within March 2022.
Vertical C: Test rig development is underway, a straddled rotor concept selected to forward with. A Ph.D. student is hired for the project. The student has completed the relevant course work and is currently doing the literature survey for the project. Rotor dimensioning and bearing placement to provision a subcritical rotor design is underway. Work also started on computing aero loads on seal to account for total torque needed for drive motor selection.
Vertical D: Choice of electric machine for starter-generator application The possible candidates for the application of starter-generator in aerospace applications are: • Wound Rotor Synchronous Machine (WRSM) • Induction Machine (IM) • Switched Reluctance Machine (SRM) • Permanent Magnet Synchronous Machine (PMSM) PWhen compared, different machines have their own advantages and disadvantages as listed below:
Type | Advantages | Disadvantages |
---|---|---|
Wound Rotor Synchronous Machine | Fail safe Good efficiency | Low power density Increased mechanical Complexity |
Induction Machine | Fail safe Low efficiency compared to PM | Ability to sustain high rotor temperature Lagging pf simple flux-weakening control |
Permanent Magnet Synchronous Machine (PMSM) | High efficiency and power density Not a fail-safe machine | Demagnetization at high temperature, high cost, poor availability of magnetic material |
Switched Reluctance Machine (SRM) | Fail Safe Low efficiency | High torque ripple, high acoustic noise |
Based on the comparison made above induction machine is selected for application.
Following are the different types of induction machines are being considered for the application:
- Dual Winding Induction Machine (DWIM)
- Open Winding Induction Machine (OWIM)
- Multiphase Induction Machine
- Brushless Doubly Fed Induction Machine (BDFIM)
Infrastructure developments
Vertical A: The heater system required for the high pressure heated air supply is ready at NCCRD. It is being tested currently for required flow conditions. Funding for this was through a UAY project.
Vertical B: 50kW oil heat loop commissioned at the NCCRD ground floor. Commissioning of 20kW chiller loop is ongoing.
Vertical C: The purchase process of two shakers with control panel is completed. They have been shown to work at the vendor site. The shakers have been received at IITM and are awaiting installation at NCCRD.
Vertical D: No infrastructure required for this vertical in Phase 1.
Output
- IRIS Webinar held in Aug 2021, a link to the recording of the webinar, is provided above. The Webinar was attended by more than 150 attendees, and had a very good interaction session with some thought provoking questions. Our pCoE took part in the energy summit conducted on 14-16 Dec 2021, at IITM Research Park, by the IITM Energy consortium and deliberated the ways in which hydrogen economy can be sustained in India. This event was well attended and was widely publicised in social media and also through emails.
Mobility
- GE Aviation team’s visit to IIT M campus is tentatively scheduled in February. Interactions with PI, co-PI and senior engineers for GE team is also expected to happen during the visit.
Relationship
Industrial Engagement
GE Aviation, GE GRC, Bangalore, is collaborating with the IITM team in the design of the rig and combustor. The rig, when designed, will also be safety checked by the GE Safety team independent of the IITM team. The focus is currently on the design of a versatile rig within the budget.
GE Aviation is currently providing technical support for the commissioning of the CO2 test rig. Weekly review meetings with GE team are being held to ensure a steady progress on this project. GE Aviation and IIT-M is jointly developing the research plans for the development of additively printed heat exchangers to be tested once the rig is operational. Present focus is on the design of experiments.
GE Aviation, GE Global Research Campus, Bangalore is collaborating with this work by providing industry experience. They also contribute towards development support and fabrication. General Electric (GE) Aviation has set weekly meetings for the progress.
University Engagement
Once the test rig is commissioned, IIT M team is planning to expand the project scope to include development of transcritical CO2 power systems for waste heat recovery applications. This includes
- modeling, development and testing of advanced cycle architectures.
- Compressors and high pressure radial turbo-machines for CO2 power systems.