Project
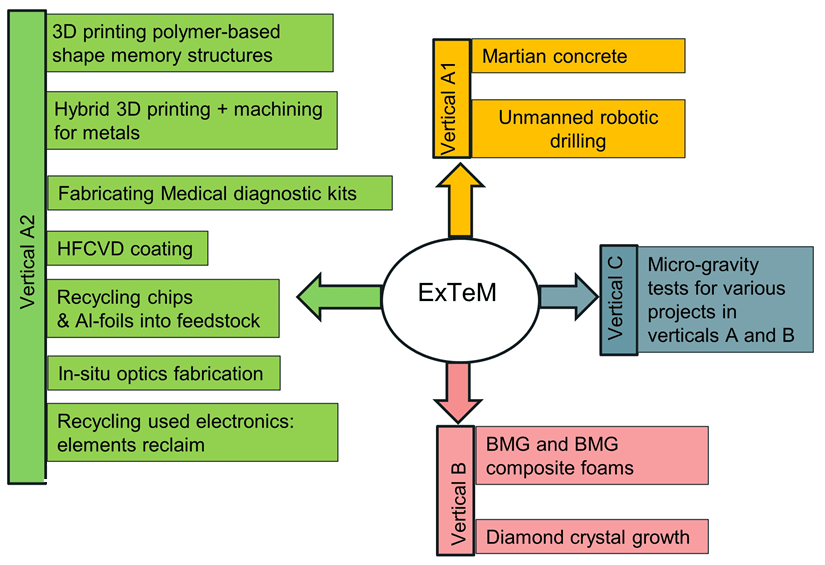
The infrastructure development, mining, and design of machines for fabricating on-board requisites will be considered in Vertical A. The infrastructure for human settlement is tackled by developing a novel Extra-terrestrial concrete that does not need water. The mining aspect is addressed by proposing an unmanned drilling system, that can be remotely commanded from the earth and should work in a smart self-correcting way without breaking drills or changing drills suitably to deal with the unknown sub-surface soil encountered. To fabricate tools or replacement for damaged parts, the design of machining systems which can handle subtractive (e.g. milling) and additive process (Metal/ Polymer 3D printing) is investigated.
The harsh space environment such as extreme temperatures, vacuum, micro gravity is always considered adversely, but converting one or more such factors to our advantage is a key aspect of vertical B. Normal gravity tends to affect the quality of processed materials such as crystals and bulk metallic glass materials. To tackle this problem, space factory will help to nullify this effect and produce materials for earth, utilizing the raw materials transported from both earth and available locally in space.
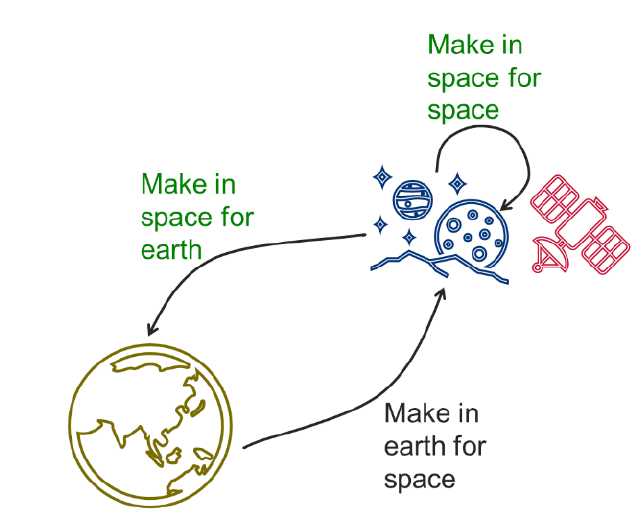
(a)
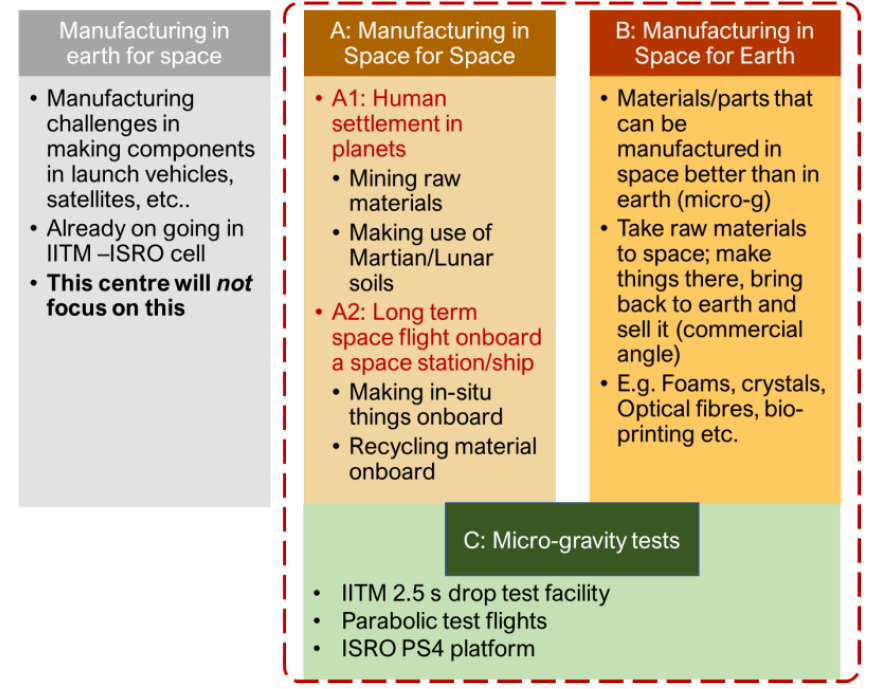
(b)
Figure (a) Different aspects of space-related manufacturing (b) Various verticals to address manufacturing in space
To materialize these research activities, test setups such as the drop tower test and parabolic flights are considered. Initial phase the tests are planned to be conducted in drop test (2.5s of microgravity) and next phase in parabolic flights. By these research activities, the centre can serve as a foundation for decades of exciting explorations that are bound to be in the international limelight.
Space manufacturing requirements into three types : (i) manufacturing in earth for space use, (ii) manufacturing in space for space use and (iii) manufacturing in space for use in earth. Activities related to topic (i) are already ongoing at IITM with several faculty working with agencies like ISRO to design and make components and systems here on earth for launch vehicles, satellites etc. The ExTeM centre will explore projects only in topics (ii) and (iii). The two set of projects are named as Vertical A and Vertical B for clarity and Vertical C involves the test setups to support Vertical A and B.
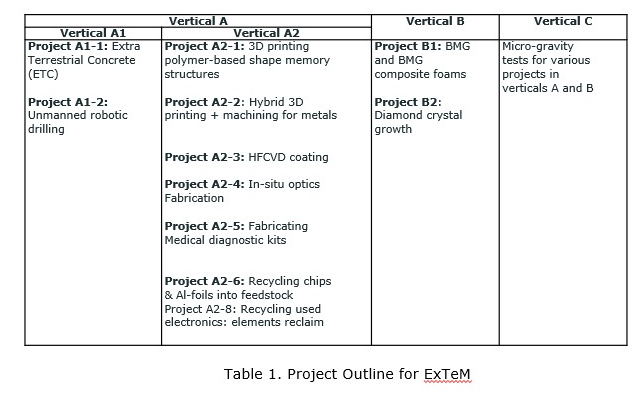
VERTICAL A1
Project A1-1: Extra Terrestrial Concrete (ETC)
Sub-vertical A1-1 will focus on technologies needed for human settlements in the moon or mars. Infrastructure is the foundation of any colony whether on earth or elsewhere. Concrete is a potential choice for infrastructure development
- Objectives (Phase 1)
- Developing processing routes of ETC using regolith simulants
- Investigating the role of temperature on mechanical properties of ETC Objective (Phase 2)
- Assessing long-term durability of ETC
- Exploring 3D printing application of ETC
- Investigating the influence of micro-gravity environment on ETC properties
Project A1-2: Unmanned robotic drilling
This project seeks to develop tools for automated remote drilling on extra-terrestrial planetary surfaces, with special attention to the Moon and Mars. One of the major challenges in such remote drilling, is that the rebound forces acting on the drill-bit as well as the drill-shaft are unknown and can be dynamic. The project will study in particular, the use of waveguide ultrasonics for sensing and feedback control of the drilling process.
Vertical A2
Project A2-1: 3D printing polymer-based shape memory structures
Shape memory polymers finds wide applications in surgery, textile, automobiles, and aerospace. It can also be used in foldable structures to minimize space requirements during transportation (space missions) and can be retracted back whenever needed. In Phase I, the materials will be fabricated through conventional route as well as by AM and all required characterization studies will be carried out to ensure the proper processing route for the space environment. In phase II, the shape memory effect of different structures for the space environment will be developed and demonstrated.
Project A2-2: Hybrid 3D printing + machining for metals
To realize a single station, a multipurpose hybrid manufacturing facility (HMF) with on stage metrology for manufacturing of parts required in the micro gravity (MG) environment is proposed. The stage I targets to understanding the behaviour of manufacturing modules in the MG towards operate them in the MG.
The AM module includes micro-plasma based Directed Energy Deposition process with alloys wire as a feedstock for manufacturing the target components. Similarly, the SM modules comprises a tabletop mill-turn machining system for producing prismatic and rotationally components and also finishing the AM printed components.
Project A2-3: HF/MP CVD coatings in micro-gravity environment (linked to Project B2)
The current method of generating water onboard using the Sabatier process produces methane as a by-product. Hydrogen is also available as a by-product and as a source on-board. Hot Filament CVD process is routinely used on earth using methane and hydrogen as feedstock to make diamond coatings on various substrates and hence is a possible way to reuse the methane. The effect of micro-gravity by studying the temperature data and atomic species concentration will be studied (feasibility study).
Project A2-4: In-situ optics fabrication
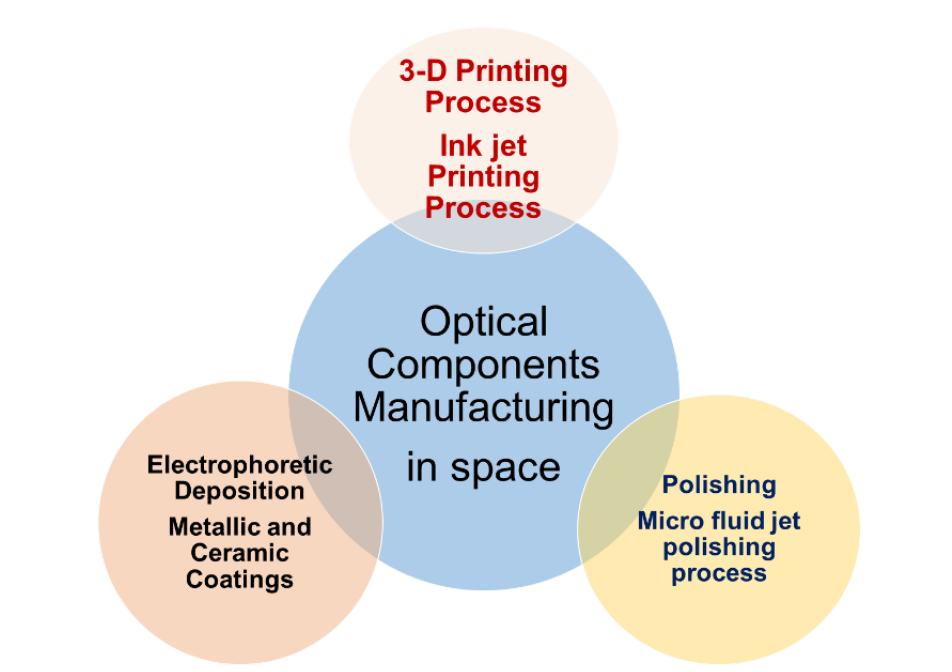
The project first focusses on developing 3D printing technologies for making of complex optical substrates/components in space. The other important focus would be on developing micro polishing systems with integrated measurement tools to assess the quality of the created products. Finally, the interest is on developing coating technologies involving ceramics, oxides and diamond proposed for protecting the mission critical components and tailoring their performances to achieve planned mission targets.
Project A2-5: Light-Actuated onboard In-situ medical diagnostic and chemical analysis kits for space travel
The project involves the development of the light-responsive LC thin films which can be deformed based on the wavelength of the light source. The project also involves detailed computational modeling to understand the deformation mechanisms of LC thin films under various geometry, boundary and source conditions.
Project A2-6: Recycling chips and foils into feedstock
To enable ExTeM through in-situ resource utilization (ISRU) technologies, an affordable, cost effective and sustainable waste management is of critical importance, promoting reuse and recycle of e-waste towards a circular economic model. The proposed research shall be used in recovery of precious metal from varied electrical and electronic waste components, such as cathode materials in Li-ion batteries, printed circuit boards, and rare earth metals (REE) from lamp phosphor and magnets
VERTICAL B
Project B1: BMG and BMG composite foams
Outline:
- To develop a foaming process for BMG and BMGMC to be produced in space for space applications
- To study the mechanical and machining properties of foams
In Method I, a Pd based bulk metallic glass will be chosen to experiment for foaming in microgravity lab at IITM. The precursor and the Pd-based BMG foam fabricated through thermoplastic expansion compared with an ingot of the same alloy and mass, but with 0% porosity as shown in Figure 1 [1]. In Method II, Rapid discharge forming (RDF) will be explored to heat and thermoplastically process a BMG in milliseconds, which takes advantage of the near constant resistivity as function of temperature in metallic glasses to create uniform volumetric heating.
Project B2: Diamond crystal
This project would follow from the fundamental studies carried out in project A2-3 and focus more on full diamond crystal growth and study the effect of micro-gravity.
Project C: Micro-gravity tests
- Year 1 and 2 will involve building of several microgravity experiments (see Table 1) for test in IITM 2.5 s drop tower.
- Long duration test platform being developed in collaboration with e-plane company in the first 18 months. Demo test will be carried out on unmanned flight in India.
- Parallelly long duration microgravity test will be carried out during the second half of year 2 in parabolic manned flights using platforms in US & Europe.
- Based on outcome of flight campaign in year 2, test rig and test setups will be modified for further 3 day flight campaigns in year 3, 4, and 5. If successful indigenous unmanned flight can also be used for further microgravity/sub-gravity tests.
Current status
Collaborations
International Collaborations
Dr. Gerhard Wilde, Institute of Materials Physics, University of Münster, Germany link
Dr. Ralph Lindken, Institute of Thermodynamics and Fluid Mechanics, Bochum University of Applied Sciences link
Dr. Sergej Hloch, Director of the Institute of Advanced Technologies, Technical University Kosice, Slovakia link
Dr. Frank Pude, Scientific Advisor, Inspire AG (ETH Zurich), Technoparkstrasse 1, 8005 Zurich, Switzerland link
Dr. Jana Petrů,Head of Department, Department of Machining, Assembly and Engineering Metrology, VST-TU Ostrava, Czech Republic link
Dr. Konrad Wegener, ETH Zurich, Switzerland link
Dr. Shanmuga Kumar, Reader in Composites and Additive Manufacturing, U. Glasgow, UK link
External international site links
International education programs
- Webinars are planned with relevant experts.
- To conduct Asia Microgravity Symposium (AMS) 2023
Industrial collaborations
Societal impact
Since the work proposed is very novel and one of a kind, it will attract young minds to come and work in this center. The centre projects will motivate/interest in young generation towards space science and technology. Such research opportunity will now be available to any qualifying student. Besides, outreach 32 activities will be conducted to engage local schools and instill in them the excitement that space-utilization has to offer.
Sustenance statement
Given the exciting developments in space activities around the world and in India, one can expect the centre activities to continue for several decades. ISRO has already expressed interest in the centre and will consider collaborating with the centre based on the outcomes. The centre will continually engage with ISRO from its initial phase and seed new projects based on the demand. By Year 2 we will hold a workshop and showcase the projects to ISRO and other relevant private partners. The centre will also actively seek funding from private players who need to develop technologies for ISRO for human life support for long term sustenance in space. The centre will make active effort to facilitate technology transfers by show-casing the on-going prototypes of machines (e.g. hybrid additive-subtractive) and processes at relevant tech-events around the country.
There will also be some startups which will come up with similar plans in the future and this center will train the personnel for them. Most startups will not have a drop tower facility for initial tests and thus this center will be unique with this capability. Further, since this idea is novel and there is no competition, the platform will attract researchers to come to India and use this platform for their research, until such platforms are being developed in their country. Thus, there is a revenue generation front for this center from this platform for the next decade. The facility will also be open to national and international researchers at slightly higher rates.
Technical/ Scientific Progress
New work done in the project
The projects under ExTeM are divided into 3 verticals designated as A, B, and C. The projects under Vertical A deal with the manufacturing technologies needed for settlements in other planets, natural satellites and asteroids (A1), and manufacturing technologies for on-board use (A2) such as hybrid 3D printing-machining, coatings, and relevant recycling technologies. The projects under vertical B explore the advantage of using microgravity for fabricating better quality materials. Vertical C deals with microgravity tests in the drop tower at NCCRD at IITM and also exploring other options such as parabolic flights. The following are the updates regarding the technical achievements in the projects so far.
Vertical A1
Project A1: Martian concrete (Investigators: Piyush Chaunsali (CE)) For colonizing extra-terrestrial places, infrastructure development using local materials is a key step. As a part of this research initiative, Martian concrete was developed without the use of water. Martian concrete showed rapid hardening and attained maximum compressive strength of about 20-22 MPa. Current efforts are directed toward examining durability of Martian concrete in varying temperature conditions.
Project A1-2: Unmanned robotic drilling (Investigators: Prabhu Rajagopal (ME) and Sathyan Subbiah (ME)) The problem statement is identified: Exploration of Olympus Mons region (the largest peak in the Solar system) in Mars. Literature surveys of NASA Mars missions, especially Curiosity and Perseverance, are conducted. Martian surface conditions and the Olympus Mons region are analyzed in detail through literature. Detailed studies are done regarding the Percussion, the drilling of the martian soil sample, and the collection mechanism and control system. The initial design of the Percussion and drilling mechanism is developed with brainstorming. The Rover design is in progress where the overall CAD modeling and finalizing of the steering mechanism, arm controller, and payload positioning are being done.
Vertical A2
Project A2-1: 3D printing polymer-based shape memory structures (Investigators: R Velmurugan (AE), R Sarathi (EE) in collaboration with Dinesh, (Fabhead; startup) and S Kumar (Glasgow, UK)) Polymer composites have this shape memory property which can be used for space structures for contraction or expansion of structures or structural systems. Suitable materials are identified, and basic characterization studies are going on. The shape memory properties are also studied.
Project A2-2: Hybrid 3D printing + machining for metals (Investigators: Sivasrinivasu (ME), Murugaiyan (MME), Sourav Rakshit (ME), Sathyan Subbiah (ME),Ramesh Babu (ME), in collaboration with AMTDC) The objective of this project is to develop a fully integrated hybrid manufacturing facility with wire arc additive manufacturing module, subtractive (milling/grinding) and inspection modules. As a part of this, the influence of gravity on the metal droplets transfer in wire arc additive manufacturing of components in space has to be investigated. As a first step, the effect of microgravity on metal transfer is studied in the Gas metal arc welding (GMAW) process using the existing drop tower at NCCRD. For this experiment, a welding machine with UPS (batteries included), high speed camera, along with other sensors and communication devices are secured using appropriate fixtures inside the capsule. This capsule along with the outer capsule will be dropped in the microgravity tower where the droplets behavior and force balance in reduced gravity for duration of 2.5s will be studied. Presently the setup is ready for the first trial. Before that initial sequencing of events, communications are being checked.
Project A2-3: HF/MP CVD coatings in microgravity environment (linked to Project B2) (Investigators: Arunachalam (ME), Ramachandra Rao M S (PH), Sathyan Subbiah (ME) in collaboration with Space Foundry (Ram Prasad Gandhiram) and Diwakar (JNCASR)) Diamond coatings/growth in outer space using Hot Filament CVD or DC plasma CVD is the objective of this project. As a first step, the behavior of DC glow discharge plasma in the microgravity environment has to be investigated. So, a glass tube with stainless steel electrodes, high voltage DC supply and vacuum pump is designed and fabricated. Next step will be to generate DC plasma and evaluate the difference in terrestrial and microgravity conditions (drop tower) using appropriate plasma diagnostics such as probes.
Project A2-4: In-situ optics fabrication (Investigators: Arunachalam (ME), in collaboration with Diwakar (JCASR)) This project aims at developing a 3-D printing system to use in the space for printing of optical components in space. In this project, the main challenge is to create a precise and uniform droplet formation from the nozzle in microgravity. The numerical simulation of the process was carried out using a multi-physics framework. An inkjet nozzle that forms a droplet in response to the driving signal was simulated considering a level set approach for liquid and air interface. The primary results obtained using the COMSOL software was encouraging and the final simulation with proper environmental variables is under progress. Also, the experimental setup that will aid in evaluation in the drop tower under microgravity is under progress. The collaborator Dr. Diwakar’s own setup has been accepted for flying the upcoming Gaganyaan mission; hence, via this collaboration the team has much to learn.
Project A2-5: Light-Actuated onboard In-situ medical diagnostic and chemical analysis kits for space travel (Investigators: Ratnakumar, A. (ME)) The light responsive thin films are fabricated. The mechanical, optical and thermal characterization of these films is in progress. The simulations on fluid-structure interaction are carried out and their analysis is being done.
Project A2-7: Recycling chips and foils into feedstock (Investigators: Sushanta K Panigrahi and Sathyan Subbiah) This project is intended to: (i) establish energy efficient novel microwave based manufacturing process to recycle metallic chips into useful products such as sheets/ wire/feedstock for additive manufacturing, (ii) establish the scientific knowhow for microwave interactions with chip bonding mechanisms for different types of chips with varying chemical composition and (iii) study the structure-property-manufacturability correlation via extensive microstructural characterization (SEM, TEM, EBSD etc.) and mechanical testing in order to understand the microwave related processing parameters. This work is in the initial stage of progress.
Project A2-8: Recycling used electronics: elements reclaim (Investigators: Kothandaraman) Growing electronic and automobile industries generates a pile of battery waste. Therefore, it essential to introduce recycling techniques suitable for this new age batteries. Herein, we introduce non-ionic deep eutectic solvents (ni-DESs) for recovering and recycling of critical metals from spent lithium ion batteries (LiBs) The extraction efficiency of this ni-DESs was more than 90% at 180°C for cobalt and lithium from the lithium cobalt oxide (LCO). Using the extracted materials, LCO was made again and used in a coin cell as cathode material. The recovered LCO material delivered 110 mAhg-1 with stable (99 %) coulombic efficiency (Fig. 1), which is on par with the capacity of the commercial LCO. Use of ni-DES will be a successful green alternate to traditional methods for recycling and recovery of critical metals from LiBs.
Vertical B:
Project B1: BMG and BMG composite foams (Investigators: Shankaran, Sathyan Subbiah) The aim of this project is to develop a foaming process for the Pd based BMG material. A single cartridge heater setup is designed and fabricated to heat a copper rod where a sample is placed inside a quartz tube, so that expansion can be viewed. As a first step to understand the foaming behavior in drop tower where 2.5 seconds of microgravity is achievable, zinc metal foaming process is chosen to study. Zinc precursors were prepared using powder metallurgy route and the samples were cut to the quartz tube dimensions so that expansion is feasible only in one direction. Next step will be to foam the zinc samples in the terrestrial and microgravity environment. The expansion rate and the foaming stability is studied using the images acquired from the High-Speed Camera. If possible, a portable x-ray machine will be installed inside the capsule to capture the foam cells clearly. Once these trials are completed, similar steps will be applied to BMG foaming.
Project B2: Diamond crystal (Investigators: Arunachalam (ME), Sathyan Subbiah (ME), Ramachandra Rao (PH) in collaboration with Ram Prasad Gandhiram (Space Foundry) and Diwakar (JNCASR)) This project is connected to Project A2-2. The updates of A2-2 are applicable for this project too.
Vertical C:
Project C: Micro-gravity tests for various projects in verticals A and B (Investigator: Amit) The capsule used for drop test is modified by machining the decks and fabricating fixtures to keep the experimental setup inside the capsule intact. Presently the experimental setup is ready for Project A2-2 and in progress for Project B1.
Infrastructure developments
Infrastructure developments related to all the verticals are listed below. Items purchased under the CAPEX are TransSteel 2200 welding setup (Project A2-2) , microplasma torch (Project A2-2), workstation (Project A2-5), Ion Chromatography (Project A2-8), compact heating setup for foaming (Project B1) and Cydock coupling (Project C). Items for which PO is issued. Ultrasonic pulser receiver (A1-2), Twin screw Lab extruder (A2-1),3D printing system and xyz stage (PO is in process) and Electrochemical Potentiostat (A2-4).
In general, the infrastrucutre at the micro-gravity drop tower facility has been bolstered heavily to support the ExTeM activities. This would be a major infrastructure contribution via the funds of ExTeM.
Output
As part of ExTeM monthly series called SpaceTalks, a series of webinars were conducted to gain insight into the current trends in the fields related to space manufacturing. This free webinar talk series is open to all and the flyers regarding the webinars are posted in the IITM social platforms and sent to researchers working in related fields. All the webinars were followed by a Q&A session, where all participants had a chance to interact with these experts.
In June 2021, Prof Gerhard Wilde from University of Muenster (Germany) gave a talk on ‘Relaxation and Deformation of a model glass-forming alloy’. This talk covered the aspects of the bulk metallic glasses Pd40Ni40P20 subjected to external shear stresses and discussion about foaming in microgravity (Project B1).
In July 2021, Dr. P. V. Venkitakrishnan, Prof Satish Dhawan Scientist, ISRO HQ Bengaluru, India gave a talk on the topic ‘Techno managerial challenges faced in aerospace manufacturing’. His talk covered widely the trends in the field of space manufacturing and also about the upcoming Ganganyaan mission.
In August 2021, Dr. Shanmuga Kumar, Reader in Composites and Additive Manufacturing,University of Glasgow, UK, gave a talk on the topic ‘Multifunctional Materials and Composites Enabled by 3D/4D Printing and Nanoengineering for Space Applications’ (Project A2-1).
In September 2021, a webinar was organised on the topic ‘Non-traditional Machining of Diamond and Diamond-like Carbon for In-space Manufacturing (ISM)’ by Dr. Ajay P. Malshe, R. Eugene and Susie E. Goodson Distinguished Professor at the School of Mechanical Engineering, Purdue University. This talk was helpful to understand the future scope in the field of space manufacturing. (Project A2-3)
In October 2021, Dr. Diwakar S. Venkatesan, Assistant Professor, Engineering Mechanics Unit, JNSCR, Bengaluru, India gave a talk on the topic ‘Evolution of Faraday instability in microgravity conditions’. Dr. Diwakar’s setup has been chosen to fly in the upcoming Gaganyaan mission.
In November 2021, Dr. Aloke Kumar; Associate Professor, Department of Mechanical Engineering, IISC, Bengaluru, India, gave a talk on the topic ‘Space Bricks – Towards Extra-terrestrial habitats for Humanity’. This covered his research works in the fabrication of bricks in space formed by the help of bacteria grown.
There was no talk in Dec 2021. Tentatively a talk n Jan 2022 by Dr. Ram Gandhiram, Founder of Space Foundry is being planned in 3rd week. Dr. Ram’s own setup was parabolic flight tested in Dec 2021 and he is willing to share some of his learning experiences.
All these talks are also recorded and uploaded regularly to the ExTeM youtube page. (https://www.youtube.com/channel/UCNBscRr9kqpkk985OIm1Saw).
ExTeM coordinator is in touch with IITM media cell office and a press release article on the micro-gravity tower and associated ExTeM pCoE activities has been drafted. With some due changes requested by the media cell, the press article will be released soon within the 1st quarter of 2022.
ExTeM coordinator is also looking into publishing an article in IITM tech magazine Shaastra.
Conference and Journal Publications:
(I) Project 2-1: Presented a paper in an International conference and paper is to appear in Key Engineering materials journal (ii) Project 2-2: An abstract was submitted for a special edition Journal related to space manufacturing and was accepted. However, due to delays in the drop-setup design, the full paper was not submitted. However, two manuscripts under preparation (a) Microgravity test setup and (b) Force balance in droplet detachment during gas metal arc wire directed energy deposition process. Also one conference presentation is aimed.
Apart from these, few more publications will be contributed from each project based on the outcomes.
Mobility
Visits planned for PI, co-PIs, international collaborators and students (both inbound and outbound)
As part of Project 2-1, Prof S Kumar has agreed to l visit us during July-August, 2022 and we also planned to visit during May-June, 2022. Similarly, in the project B-1, Prof. Gerhard Wilde will visit IITM related to the BMG foaming project, dates are yet to be fixed.
Based on Sathyan’s continued collaboration discussions with Ajay Malshe (Purdue University), he will be applying for mobility funds in the next call from the Office of GE.
Relationship
Industrial Engagement
In the Unmanned robotic drilling project (Project A1-2), currently in the design and development stage of the Rover. The team will approach the industries after making out first prototype.
In Project A2-1: 3D printing polymer-based shape memory structures , a plan to make a future startup is there.
Space foundry Inc. is being approached regarding collaboration in Project A2-8: Recycling used electronics: elements reclaim.
University Engagement
In Project A1-2, the work is collaborated with CFI Team Abhiyaan, IIT Madras and assigned 20 students including undergraduates, post grads and two PhD scholars.
In project A2-1, collaboration is made with Glasgow, UK and to have a joint PhD scholar with Professor S Kumar. For the project A2-2, discussions are being held with European collaborators for the feasibility to start joint courses in space manufacturing.
In Project B-1, regular meetings were conducted to discuss the BMG foaming with Prof Dr Gerhard Wilde from University of Muenster, Germany and Prof Dr. GS. Vinothkumar, SRM University, AP, India The first set of PdNiP samples have been casted in Muenster lab and has been sent to IITM for foaming trials.
Sathyan is having regular bi-weekly meetings and discussions with Prof Ajay Malshe of Purdue University (he was the moderator at IRIS webinar and also gave a talk in combined ExTeM/QuCenDiEM monthly webinar talk).. A topic of work has been identified in designing in-space factories. Malshe will be deploying a student and post=doc from his side, Sathyan will deploy a PhD student from IITM side.Four meetings have already been completed.
Updates
Relevant Updates
A plan to form an Indian professional society specially dedicated to space manufacturing is being discussed. The creation of society would help to bid and host the microgravity conference in IITM. The initial process for society creation is started.
Apart from this, few updates regarding the microgravity drop tower are planned to carry out.
- Plan to replace the operating mechanism of the platform door in the drop tower from motorized lead screw arrangement to Hydraulic/Pneumatic arrangement.
- IDT high speed camera service done by sending it to the OEM service center
- Processing the renewal of Drop tower Elevator Annual Maintenance Contract.
Also, as part of a fundraiser for the parabolic flight (where longer duration of microgravity is achievable), Guru Talks was given by Prof Sathyan to the IITM Alumni. Sathyan is also working with Dean ACR’s team on a targetted fund-raiser in the areas of parabolic flights and/or levitation based micro-gravity setup designs. And as a part of ExTeM monthly talk, speakers will continue to be invited from different fields of space manufacturing.
A formatted report of progress is available at: https://drive.google.com/file/d/10B4g488WjhuSRUhMfyERX_vpARCCx6Lr/view?usp=sharing