Project
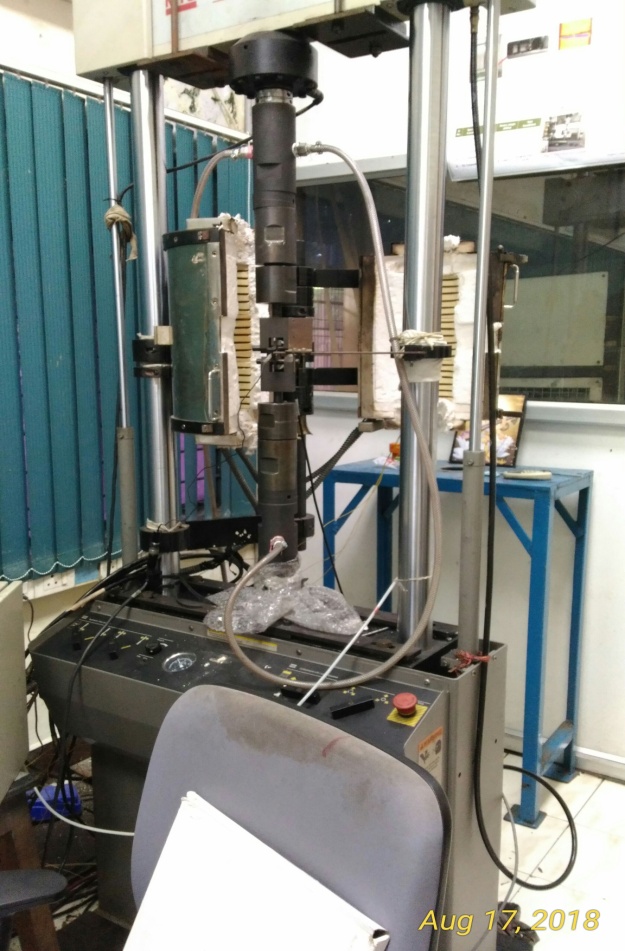
Safe operation of systems involves certain amount of risk apart from establishing the confidence level of operation. This aspect is generally handled by reliability and risk analysis experts using several techniques including probabilistic safety analysis (PSA). However, the effect of repair on the reliability of operations is not easily understood and included in the risk analysis.
The proposed CoE will bring together experts from various domains of design, manufacturing, operation and maintenance; integrate the physics of problem, probabilistic safety analysis and use Digital Twin concepts for individual asset management.
Digital Twin as the tool for asset management incorporates:
System orientation, which is more of a holistic consideration of asset systems, rather than merely considering individual components;
Risk orientation, considering risk due to uncertainties in achieving stated objectives, such as down time due to repair and maintenance which calls for a subsequent risk management approach and
Individual asset-centric orientation, like the way aircraft industry is moving towards individual aircraft tracking.
A digital twin is a digital representation of a physical object, process or service.
A digital twin can be a digital replica of an object in the physical world, such as a jet engine or wind farms, or even larger plants.
A digital twin is a computer program that uses real world data to create simulations that can predict how a product or process will perform. For example. Flight loads data after every flight mission can be fed into the digital twin model to estimate fatigue damage accumulation.
A digital twin can allow the enhancement of strategic technology trends, prevent expensive failures in real objects.
A digital twin through the use of advanced analytical, monitoring and predictive capabilities can aid to test processes and services.
Concept of Digital Twin for Life Prediction
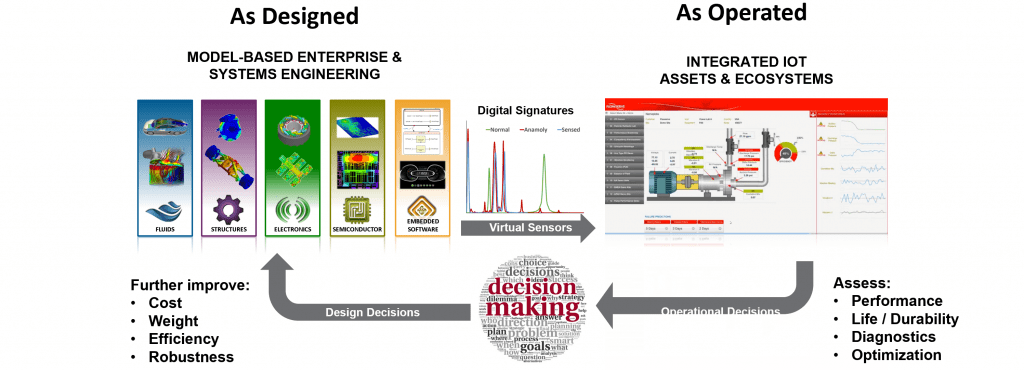
Snap shot of facilities/Results.
Research on Corrosion Fatigue Crack Growth
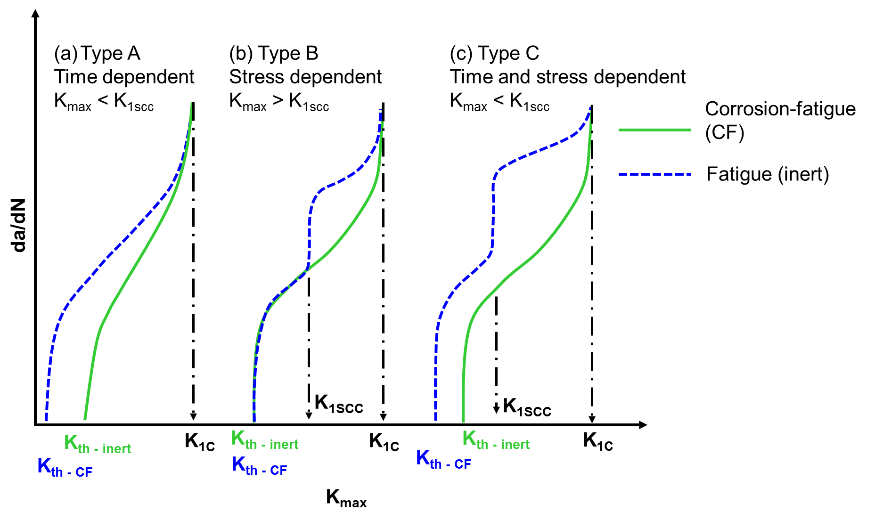
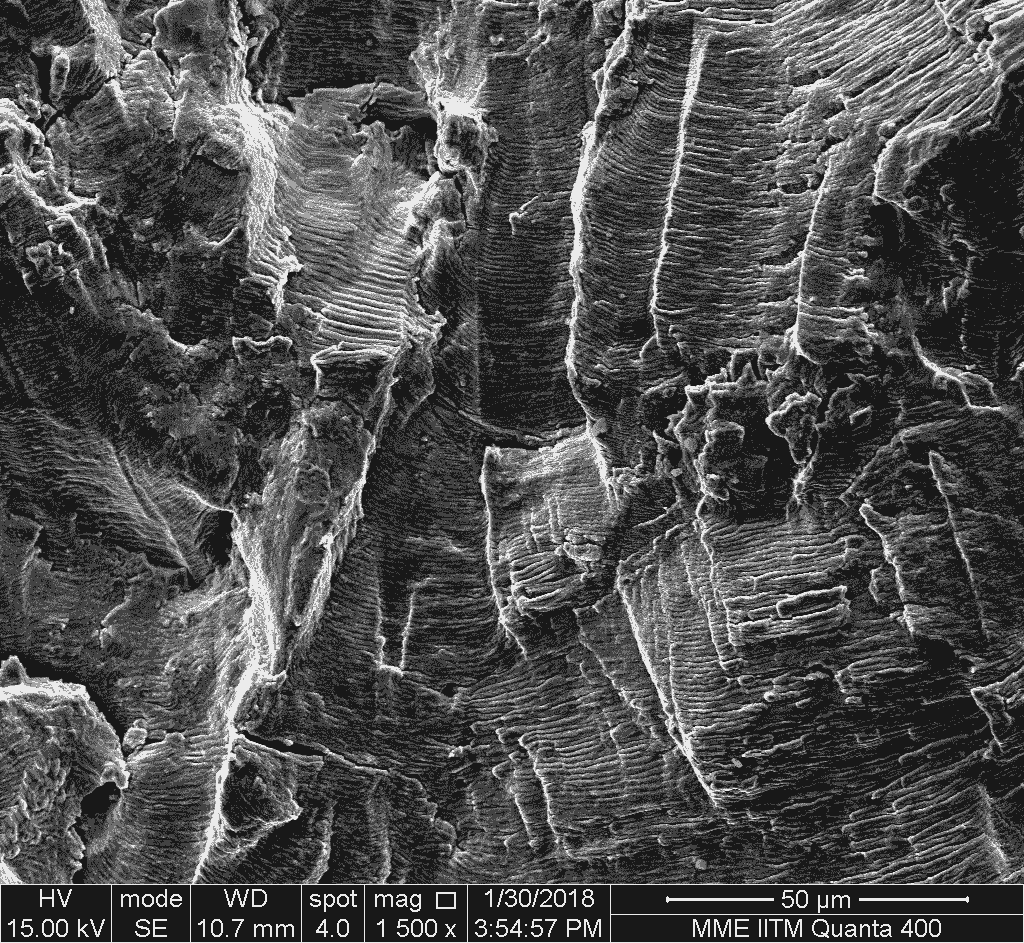

Digital Twin Enabled Life prediction.
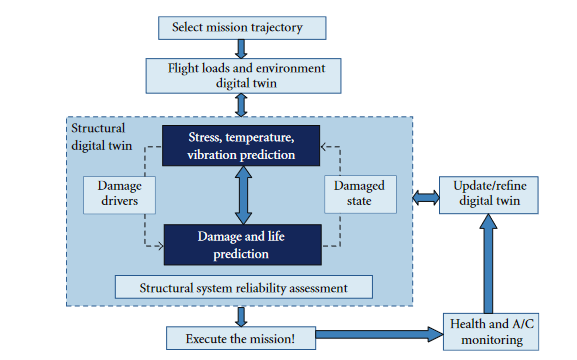
Multiscale Damage Modelling.
The Digital Twin will mimic the behaviour of its actual aircraft as much as possible. Damage tolerance checks for slow crack growth or fail safety will still be performed to ensure safety. However, only known damage will be placed in the Digital Twin for life management purposes. If damage is not known to exist at a location, a distribution of damage forming features for fatigue cracks, will be assumed at that location. In this context, corrosion pits are considered as sites for corrosion-fatigue damage initiation and growth.
The distribution and type of damage forming features is dependent on the material and its processing parameters, apart from residual stresses due to fabrication process. Physics-based models for how damage forms from these features will have to be integrated into the structural analysis.
Fatigue Modeling
- During fatigue life estimation, it is pertinent to note that fatigue crack initiation and crack growth, or other environment induced damage process, is driven by stochastic driving forces computed at the component scale. However, the component-scale model will have to be periodically updated to account for material-scale damage that reduces local stiffness, thereby, resulting in redistribution of local stress fields. The need for a stochastic, multi-scale simulation capability that integrates material performance with structural response is essential.
Reliability Modelling:
- Uncertainty Quantification, Modeling, and Control is another variable for digital twin enabled life prediction.
The safe operation of systems also involves certain amount of risk apart from establishing the confidence level of operation. This aspect is generally handled by reliability and risk analysis experts using several techniques including probabilistic safety analysis (PSA).
In case of automotive systems, the number of samples that are available for testing to arrive at a mean confidence level of operation is good, but in case of one-off designs (such as power plant systems), such a luxury to test ‘n’ components to arrive at reliability and confidence level does not exist.
Traditionally, the operators of systems have handled the problem by working in independent domains, without much of interaction. For instance, the complete record of assembly is not available to life prediction team which assumes all assemblies are having perfect fit.
Similarly repair and replacement histories are not incorporated in life revalidations. The reliability and risk re-estimation is not part of the repair and overhaul process in many cases.
Thus, one could see a big gap between the approaches followed by various domain experts to look at the problem of life estimation for reliable operation.
Probabilistic safety assessment – another input for risk informed life prediction.
Expected deliverables of the research
Establishment of a Center with initial lab facility that is working on operationalizing the Reliability & Risk program.
Initiating activities related to Digital Twin modeling, structural integrity assessment taking into consideration the manufacturing processes, component assembly history, consideration of service loads
- Lecture Courses, organization of workshops on Digital Twins, significance of structural integrity, Reliability & Risk assessment, and expert services to industries.
Initiation of Risk and Reliability lab activities
Initiation of academic program on master’s and doctoral research in Reliability and Risk assessment;
Consultancy / Expert services to Industries.
Invite Experts from India (DAE/associated establishments)
Invite Experts from abroad (Prof. Michal Pecht, CALCE, University of Maryland, USA, Prof. Oliver Straeter, U of Kassel, Germany, Jezdimir Knezevic, MIRCE Akademy, Exeter, UK to name a few).
invite other specialists from the structural integrity domain as visitors and advisors to the Center.
Academic scholar exchanges are envisaged as part of the activities of the Center.
Exchange scholars from CALCE Center of U of Maryland, MIRCE academy of UK as well as from U of Kassel.
Publications of papers and technical reports.
Current status
Procurement of capital items for Safety Critical Systems Lab in progress.
- Finalization of technical specs after interaction with prospective vendors.
Recruitment of research scholars through the July 2021 admission sessions.
Organization of Webinar jointly with SRESA, Mumbai
- One Webinar has already been organized on May 29, 2021 (virtual).
Collaborations
International Collaborations
University of Maryland, Centre for Advanced Life Cycle Engineering, Maryland, USA (Prof. Michael Pecht) (MoU approved)
Prof. Oliver Stratter, University of Kassel, Germany (MoU discussion initiated).
International education programs, conferences/seminar/webinar links
- We have hosted a Webinar with SRESA-IIRR on May 29,2021.
Industrial collaborations
CSIR-SERC/CFR, Chennai for joint training programs on reliability and risk assessment.
SRESA-IIRR joint programs.
Societal impact
Introduction of concept of digital Twin for safe operation of critical systems - such as power plants, automotive, railway, aerospace and other safety critical systems.
Integration of multi-discipline approaches to life prediction taking into consideration, the design, manufacturing process, assembly considerations, operating parameters obtained from individual systems to estimate the safety, reliability aspects of operation leading to improved risk analysis
Setting up of academic programs together with a professional society SRESA and its international collaborators.
Publications in dedicated journals of reliability, risk and life cycle analysis.
Collaboration with Reliability groups in India and abroad.
Collaboration with fatigue and fracture groups in India and abroad.
Sustenance statement
The operation and maintenance of equipment, ill be self-supported through the revenue generated from the Centre and more equipment/facilities will be added in due course of time.
Industrial consultancy projects.
Testing support.
In future, the CoE will be expanded to a more independent entity based on self-sustenance of activities and assisted by funding from Industry sponsors, and Government agencies.